DFA – Deep Field Analysis
Patented sensor technology for fast quality inspection of metallic parts
Hows does DFA work?
- Excitation with a ramp-shaped electromagnetic signal
- Formation of eddy currents in the sample
- The sensor measures the voltage-time curve of the emitted field – the inductive fingerprint
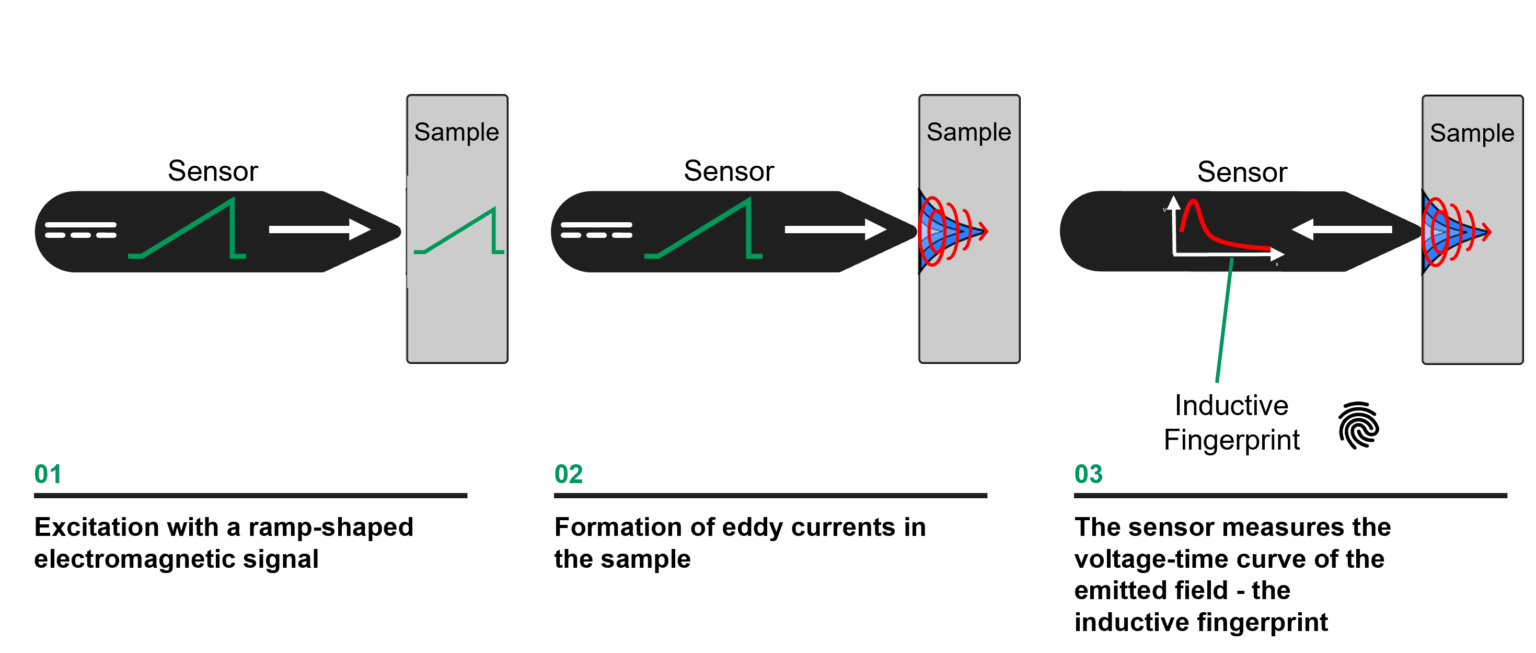
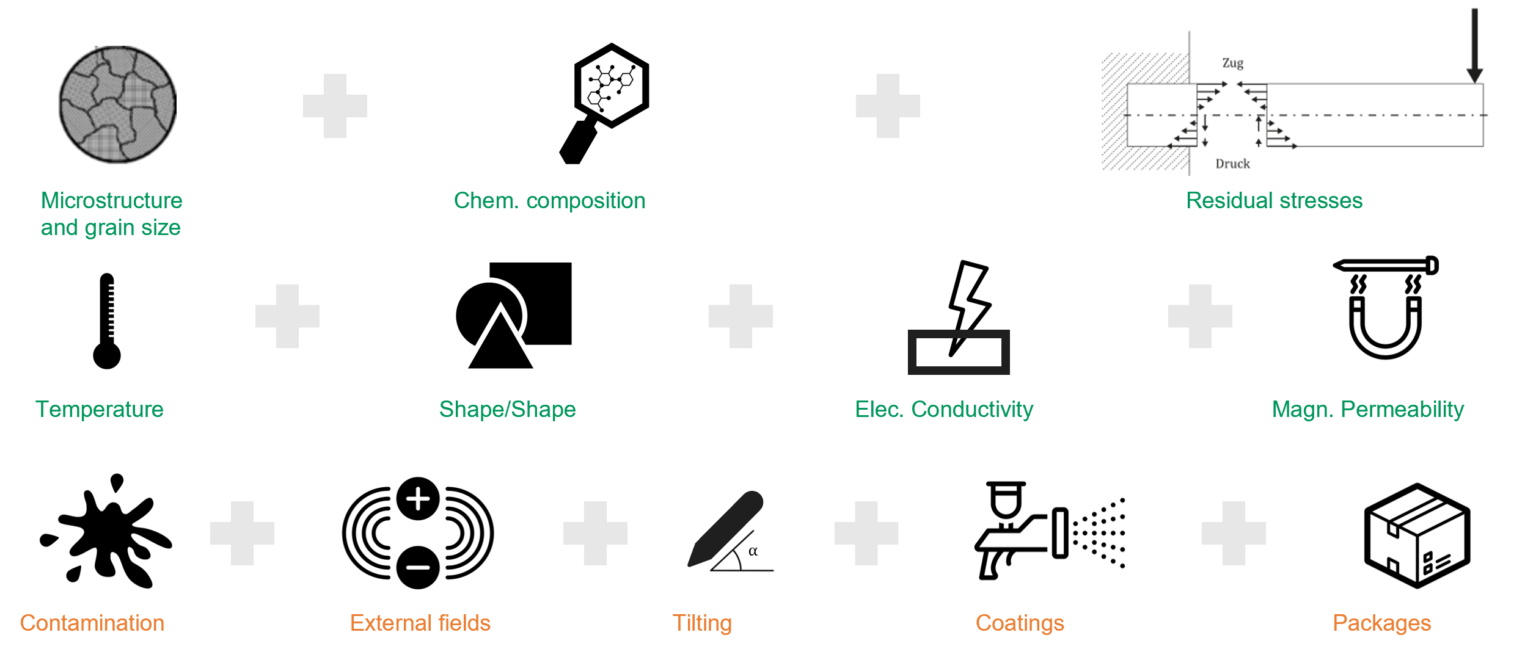
The sum of the material properties is measured, while disturbing factors are largely compensated.
What makes DFA special?
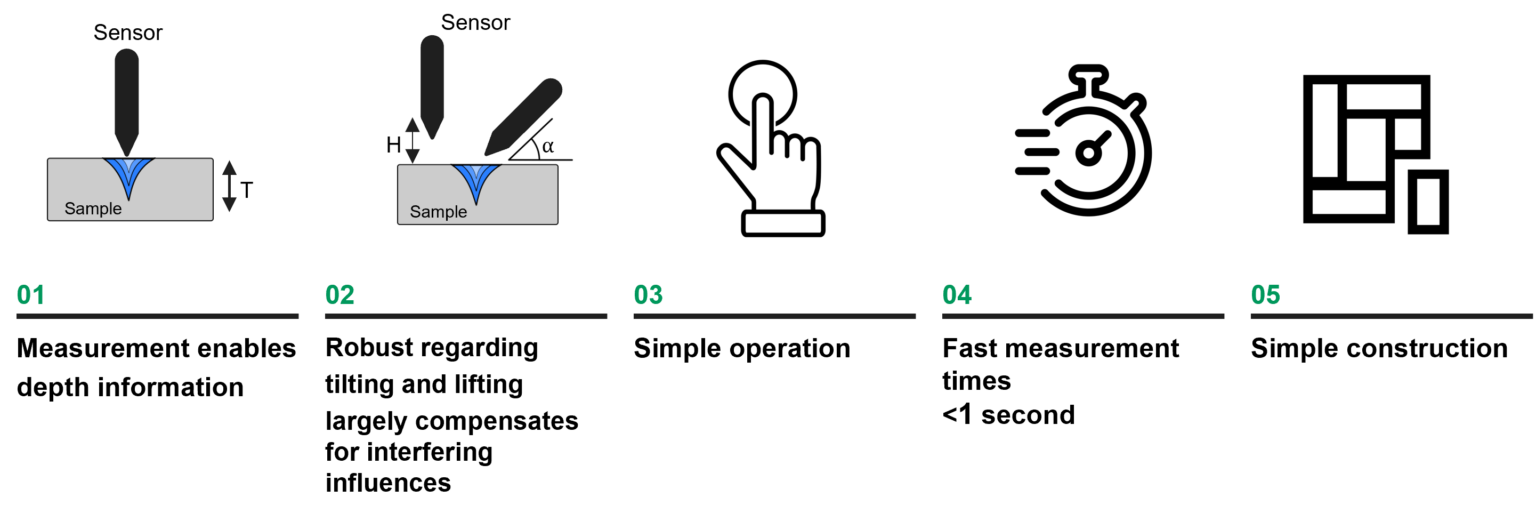
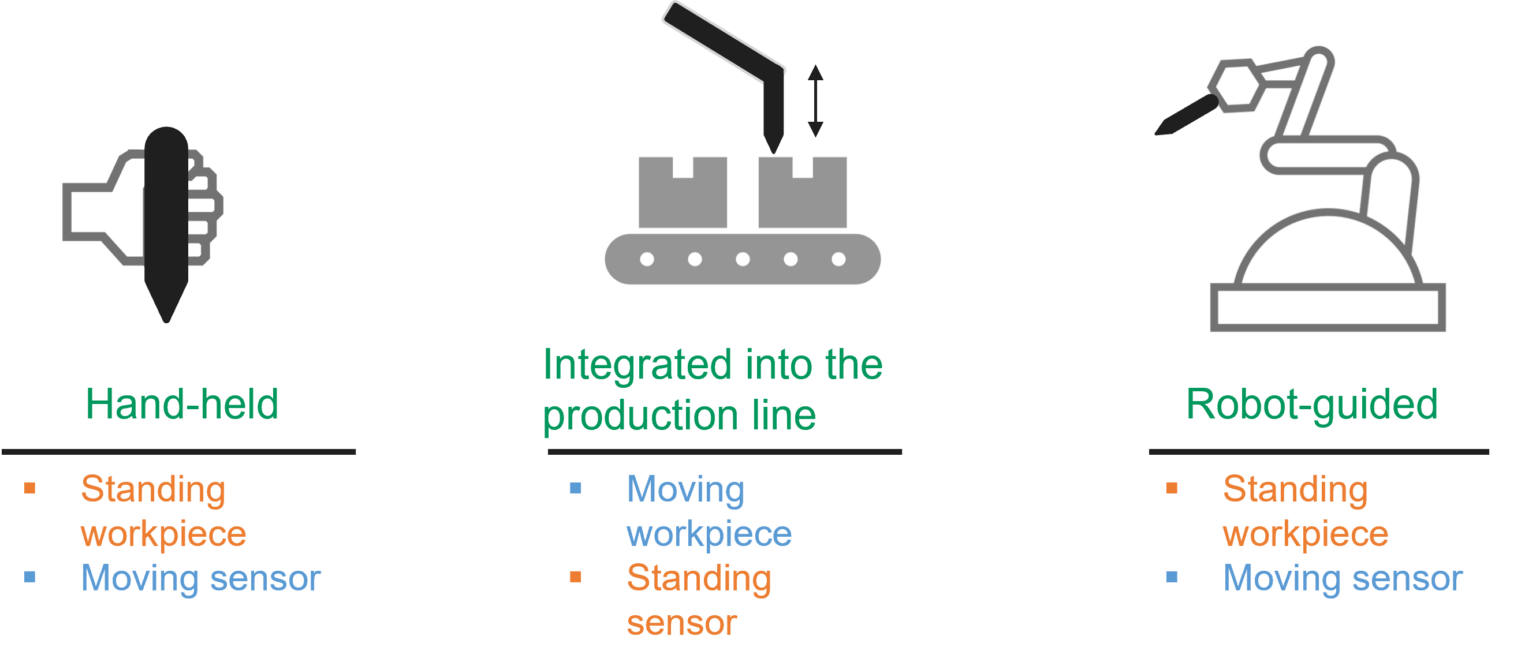
Application types
Sorting hardened gears
Application
Due to a system error, exactly 1 tooth was not induction hardened on a few parts. The fault was discovered when 90,000 gearboxes had already been delivered to the customer.
Solution
The handheld device enables fast, non-destructive and safe detection of the defective tooth
Added value
Testing possible at the customer. Avoidance of unnecessary component destruction in value of approx. 10 million EUR
100% IPC-NDT during heat treatment
Application
Monitoring of hardened and tempered steel beams. Time-consuming 100% of Brinell hardness.
Solution
Correlation of the DFA values with the Brinell measurement enables an 80% reduction in inspection time
Added Value
Personnel reduction by 50% with the handheld device. Future automation possible.
Simple testing of precious metal
Application
A large amount of gold coins to be tested for authenticity
Solution
Differences become visible through comparison with a reference coin
Added value
Testing by the customer possible with the help of a loaner device. The private sale of Krugerrand gold coins was made possible.
Hardness distribution for tools
Application
Case hardened parts are optimized. Tuning of the hardening tool.
Solution
Scanning of components provides the toolmaker with quick feedback
Added Value
Optimized component quality. Improvement of homogeneity leads to energy saving of 8%.
Sorting material mix-ups
Application
Contaminated bulk material cannot be processed automatically. Manual sorting is too expensive.
Solution
As an automated sensor, DFA detects the differences in the process Different products are monitored with the same sensor
Added value
Low-Cost Process safeguarding. Scrap avoidance
Recognizing tensions
Application
Coated films become wavy due to inhomogeneous stress conditions and elongation. Difficult web guiding and winding.
Solution
As an automated sensor, DFA also detects shape defects in metallic foils in the process. Multiple sensors monitor across the width and length.
Added Value
Significant increase in output due to improved process control.
Inhomogeneity during forging
Application
Defective spots in forgings lead to visual defects and a reduction in structural strength.
Solution
Reliable process monitoring detects structural defects even below the surface.
Added Value
Possibility of 100% control for safety-relevant components
Composite materials monitoring
Appication
In solder cladding, ensuring the correct layer structure has high priority. Mix-ups lead to high damages during further processing.
Solution
The DFA check also distinguishes several layers safely
Added Value
Increased security for the customer
Contact
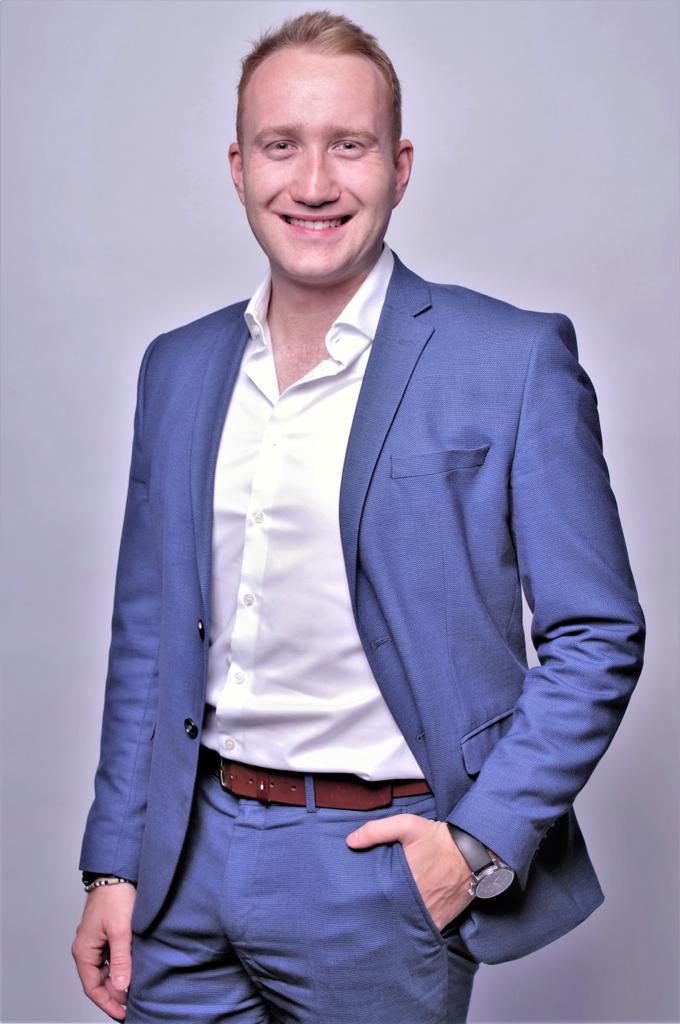